The basic principle and advantages of
ultrasonic spot welding machine:
Ultrasonic spot welder actually belongs to the category of ultrasonic welding, which produces high frequency vibration through ultrasonic wave to weld metal or plastic together.
Ultrasonic spot welding is more suitable for processing of thermoformed parts without assembly profile, or parts whose geometry and practical conditions preclude the possibility of standard welding operation.
Spot welding can be in ABS, polyethylene, polypropylene, PVC and other soft plastic sheet for ultrasonic strength spot welding. Specially designed projection head is used to enhance welding strength and appearance. Ultrasonic spot welding replaces adhesives, rivets, staples and other mechanical fasteners. This process is used to assemble trailer bodies, automotive defrosting pipes, furniture and other large thermoplastic parts. Many welds can be performed simultaneously using portable handheld tools and multi-head automation systems.
Welding principle:
Ultrasonic waves are mechanical vibrations similar to those produced by Musical Instruments. These vibrations are called ultrasounds because they have frequencies higher than the hearing of the human ear (greater than 16 kHz). In the acoustic component, these pressure waves are generated by a generator. This will send alternating current at the same frequency as the converter (or transducer). This energy is then converted into mechanical vibrations by a transducer made of piezoelectric ceramics. The mechanical vibration then creates thermal friction, which triggers the welded material molecules to start moving. Ultrasonic energy melts the point of contact between the two parts, creating a joint that quickly binds the parts together.
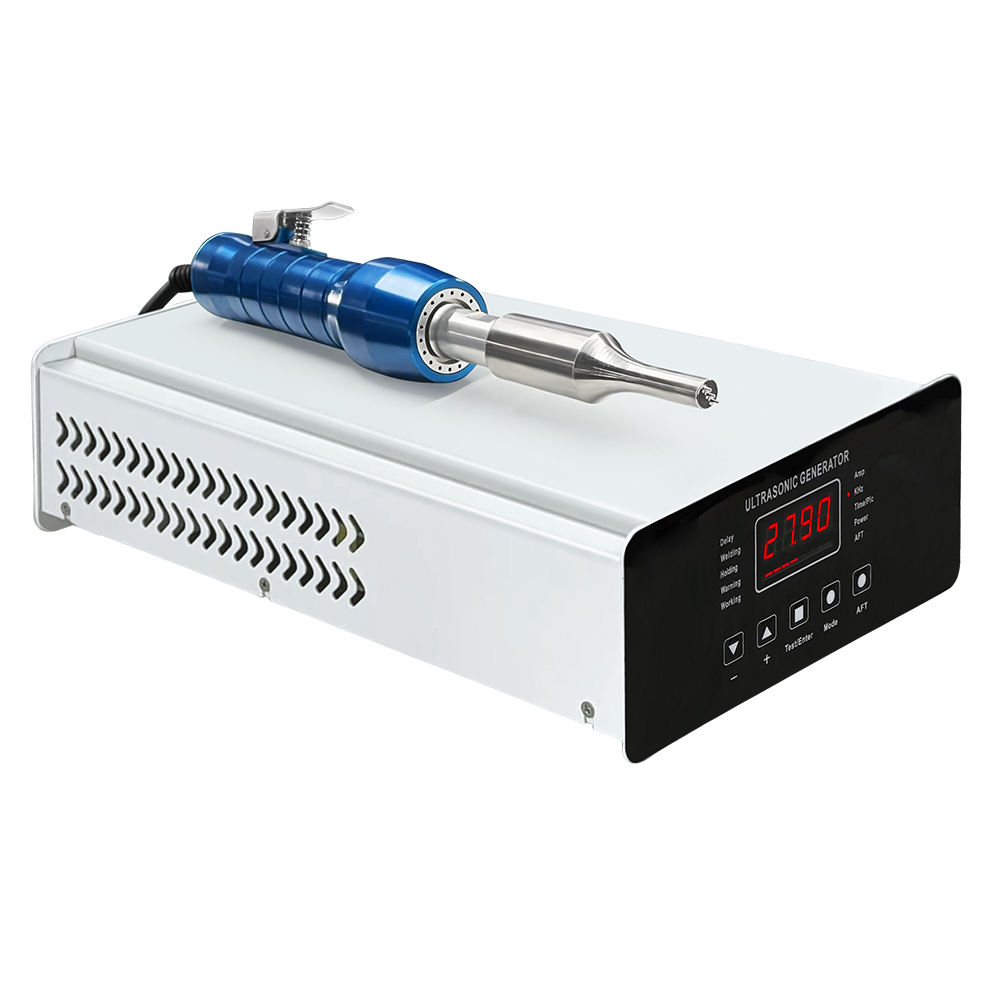